The Stock Levels report is allows you to quickly review all stock levels across multiple stores. The totals are reported regardless of whether you are maintaining stock levels or not.
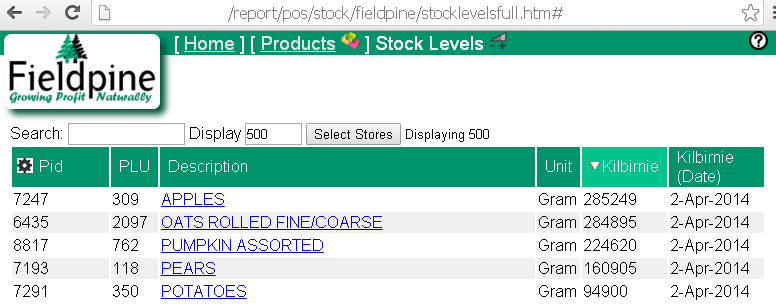
The report will automatically remove all products that have zero stock levels. This report can be saved to Excel, but if you do this remember to increase the display limit (shown as 500 in example) to include all products.
Tip: Adding more stores to the report does not greatly add to server processing time, unless you are also displaying calculated levels, BUT it can slow some browsers down as they try to draw a large table
Why are my stock levels wrong? negative?
There are many reasons that stock levels can drift and maintaining accurate stock levels requires constant effort. You need very tight processes and controls otherwise every minor anomoly will show as inventory drift. Keep in mind that for a computer system to report stock levels, you need to enter every change that would affect stock levels. Taking one item for store use is easy to do, but needs to be recorded in the system.
Some of the reasons for stock to be wrong are:
- Not recording all inwards transactions. This is not necessarily wrong, a common tactic used by retailers is to only manage stock levels for some products or departments and leave others to manual means.
- Not recording all sales, or selling the wrong product. This is more likely if you are not using barcodes
- Using stock without recording as writeoff
- Selling items as "misc" or "cash item" when there are problems selling at the checkout, but failing to later adjust the stock levels.
- Theft. By customers or staff or suppliers, or anyone that has physical access
- Incorrect data entry, such as recording against product #1 when it was product #2. The frequency of this tends to increase as the number of people performing data entry increases - different people will pick different items from a list
- Incorrect counting at stocktake time.
- Timing errors with stock counting. Especially where partial stocktakes are being performed while trading.
- Not performing / recording stocktakes. While any system should be able to balance for all time, not entering stocktakes can make this a very difficult task.
- Using a lane or store system when a head office system exists. To fully report and reconcile stock levels you need to use the main servers in your chain. A trading counter does not have or understand all the transactions.
Some less common reasons are
- Changing an items unit of measure. If a definition product is changed from "units" to "grams" this can seriously affect calculations. The system cannot understand how to convert between the two.
- Program failure. While there is always the scope for program logic to be wrong, this is typically a lot less frequent cause than people believe.
- Database failure. This is where the data in the database is corrupted, lost or similar. This can happen if you have computer failure.
- Product failure. Where the barcode or product identifiers are wrong. The product says it is "x" but actually it is "y"
- Corrections over time. If a level was manually corrected directly in the database at some point, this can lead to more problems later if the correction is done wrongly. Simply adjusting the stock level in the database will often cause this problem as the audit records no longer match the transactions.
Calculated Levels
This report can optionally display the calculated levels where the system attempts to take all historical transactions and verify this matches the reported stock level.
The report will highlight calculated levels if they differ from actual levels. The colour is used to indicate how much we trust the calculated level.
- No highlight means the level matches the actual
- Yellow highlight means we believe the calculated level is correct, but it differs from actual.
- Purple indicates that we have probably been unable to calculate the level at this time. A common cause is a stock transaction type that cannot be understood.
Calculated levels are primarily a support tool. They can be useful if you believe stock levels are wrong in the system. If the actual levels match the calculated levels then there is a very high chance that the problem lies outside the software. However, calculated levels can sometimes report discrepancies that are not real, especially if you are reporting calculated levels for products with a long life time.